On October 7, we received an inquiry from an old customer in Vietnam for flanges, forged pipe fittings, and some customized elbows. The product in this inquiry is basically the same as the previous order,and the customer is very satisfied with the previous batch of goods.
After reviewing our quotation, the customer discussed the details of the order with us, including packaging, transportation, delivery time and other issues. Finally, we received the customer’s order. This is our second cooperation with the client.
Below is purchase order list
No | Description | Material |
1 | HALF THREAD COUPLNG HEAVY SERIES EN10241-DN15 | A105 |
2 | HALF THREAD COUPLNG HEAVY SERIES EN10241-DN40 | A105 |
3 | HEX PLUG ASME B16.11 1/2″ ISO 7/1-RC 6000LB | ASTM A105 ZINC COATED |
4 | HEX PLUG ASME B16.11 2″ ISO 7/1-RC 6000LB | ASTM A105 ZINC COATED |
5 | HEX PLUG ASME B16.11 3″ ISO 7/1-RC 6000LB | ASTM A105 ZINC COATED |
6 | SCR. BUSHING ASME B16.11 1-1/2″ X 1/2″ ISO 7/1-RC 6000LB | ASTM A105 ZINC COATED |
7 | SCRD CAP ASME B16.11 2″ ISO 7/1-RC 3000LB | ASTM A105 WROUGHT |
8 | SLIP-ON FLANGE DN50 UNI 2278 PN16 FF | A105 |
9 | SLIP-ON FLANGE UNI 2278/29 DN50 PN16 RF | A105 |
10 | THREAD HALF COUPLING HEAVY SERIES DN40 EN10241 | A105 |
11 | THREAD HEX. PLUG HEAVY SERIES DN40 EN10241 | A105 |
12 | SCR. CAP 2″ ISO 7/1-RC 3000LB, ASME B16.11 | A105 |
13 | PIPE BENDING ELBOW 90 DEG. R=205 Ø88.9*3.2mm as Dwg | A105 |
Carbon Steel Forged Fittings
Threaded Fittings
Threaded fittings is a common used type of forged fittings in material of carbon steel. The threads can be NPT, BSPP, BSPT, PF, PT, MPT.
Size | 1/4” to 4”( DN6 to DN100) |
Pressure Rating | Class 2000, 3000, 6000 LBS |
Standard | ASME B16.11, BS3799, MSS SP-79 / 83 / 85 / 97 |
Type | Threaded Elbow, Tee, Cross, Cap, Coupling, Boss, Plug, Bushing and Union. |
Material | ASTM A105, A350 LF2/LF3, A182 F5, F9, F11, F12, F22, F91,A694 F42, F46, F52, F60, F65 etc. |
Inspection photos
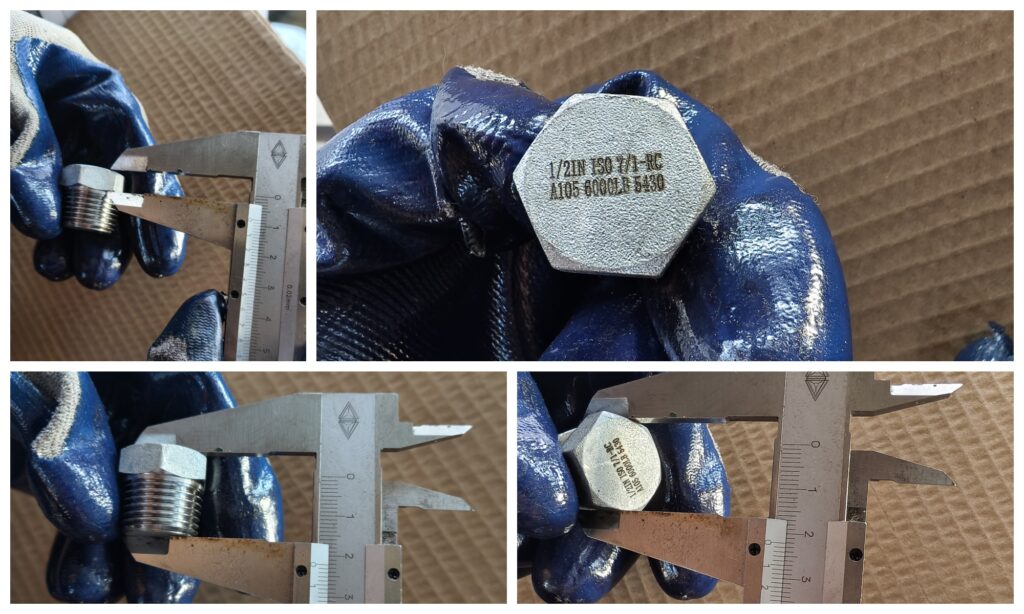
Socket Weld Fittings
Socket weld fittings are one type of high pressure forged fittings, which available in carbon steel, alloy steel, stainless steel and duplex steel. We also call it as SW.
Size | 1/4″ to 4″ ( DN6 to DN100) |
Pressure Rating | Class 3000, 6000, 9000 LBS |
Standard | ASME B16.11, BS3799, MSS SP-79 / 83 / 85 / 97 |
Type | Socket Weld Elbow, Tee, Cross, Cap, Coupling, Boss, Union, Outlet. |
Material | ASTM A105, A350 LF2/LF3, A182 F5, F9, F11, F12, F22, F91,A694 F42, F46, F52, F60, F65 etc. |
Carbon Steel Forged Flanges
Forged flanges are flanges manufactured by forging technology, which have excellent mechanical properties and reliability. The forging process makes the internal structure of the material more compact, eliminates defects such as pores and inclusions, thereby improving the strength, toughness and corrosion resistance of the flange. Forged flanges are widely used in high pressure, high temperature and corrosive environments such as petroleum, chemical, electric power, shipbuilding and nuclear industries.
Shape Type | Regular and Long Neck |
Sealing Face | RF, FF, FTJ |
Size Range | 1/2″ – 48″/ DN15 – DN1200 |
Pressure Rating | Class 150, 300, 600, 900, 1500, 2500lb |
Standard | ASME B16.5, ASME B16.47 Series A/B |
Carbon Steel | ASTM A105 / A105N |
Inspection photos
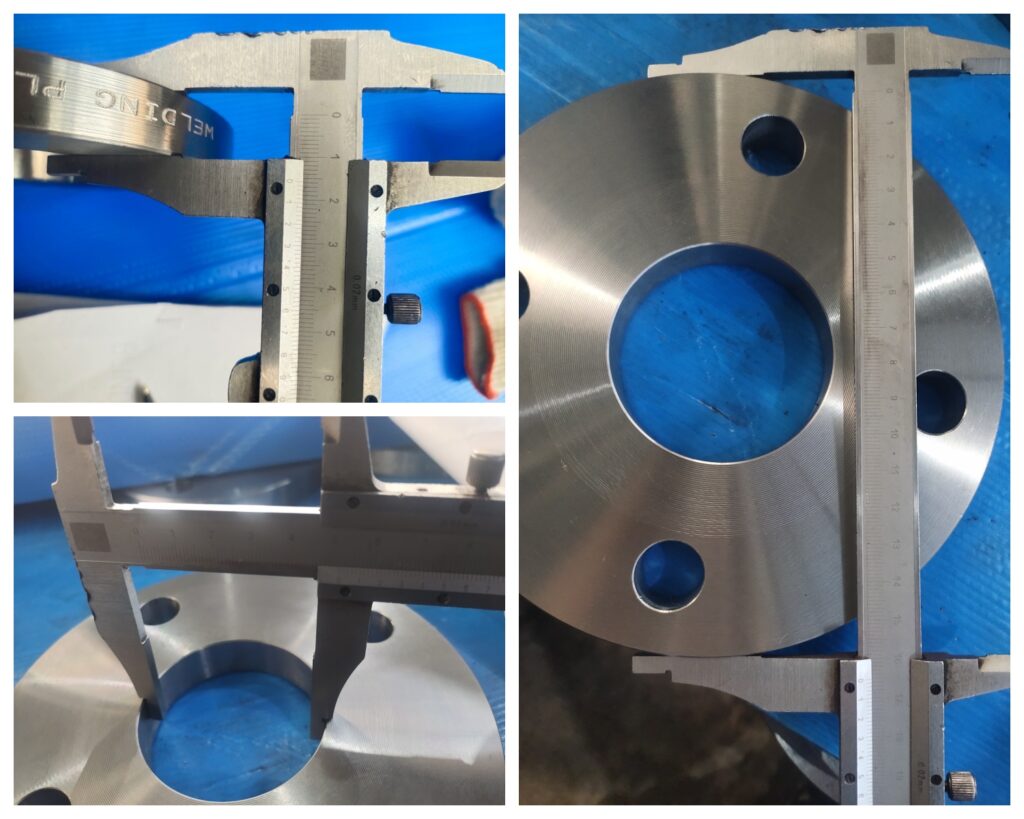
ASTM A105 Carbon Steel Forged Fittings & Flanges
Chemical Composition
CHEMICAL | LIMITS | C | Mn | P | S | Si | Cu | Ni | Cr | Mo | V |
ASTM A105 | MIN | 0.6 | 0.1 | ||||||||
MAX | 0.35 | 1.05 | 0.035 | 0.04 | 0.35 | 0.4 | 0.4 | 0.3 | 0.12 | 0.08 |
Mechanical Properties
MATERIAL | T.S (MPA) | Y.S (MPA) | EL % | R/A % | HARDNESS |
ASTM A105 | 485 min | 250 min | 22 min | 30 min | 197 max |
Manufacturing Process of Forged Pipe Fittings and Forged Flanges
The manufacturing process of forged pipe fittings and forged flanges mainly includes:
1. Raw material preparation: Select suitable metal materials, such as carbon steel, alloy steel, stainless steel, etc.
2. Cutting: Cut the raw materials into suitable lengths according to the product size.
3. Heating: Heat the raw materials to a suitable temperature for forging.
4. Forging: Forge the heated raw materials into the required shape by free forging or die forging.
5. Cooling: Cool the forgings to room temperature.
6. Heat treatment: Heat the forgings as needed to improve their mechanical properties.
7. Machining: Machining the forgings to achieve the required size and accuracy.
8. Inspection: Inspect the forgings to ensure that their quality meets the requirements.
Latest News
02 8 月 2019Copper Nickel Flanges UNS C70600Zizi offers ISO certified copper nickel flanges, stores large quantity of Cu-Ni 90/10 weld neck flan...
29 7 月 2019Stainless Steel Buttweld Fittings ManufacturerZizi is stainless steel buttweld fittings manufacturer, we offer stainless steel pipe elbow, tee, ca...
19 7 月 2019Steel Pipe Nipple Types, Dimensions and MaterialsBasic pattern of steel pipe nipple is a short piece of pipe with threads at both end or at one end....